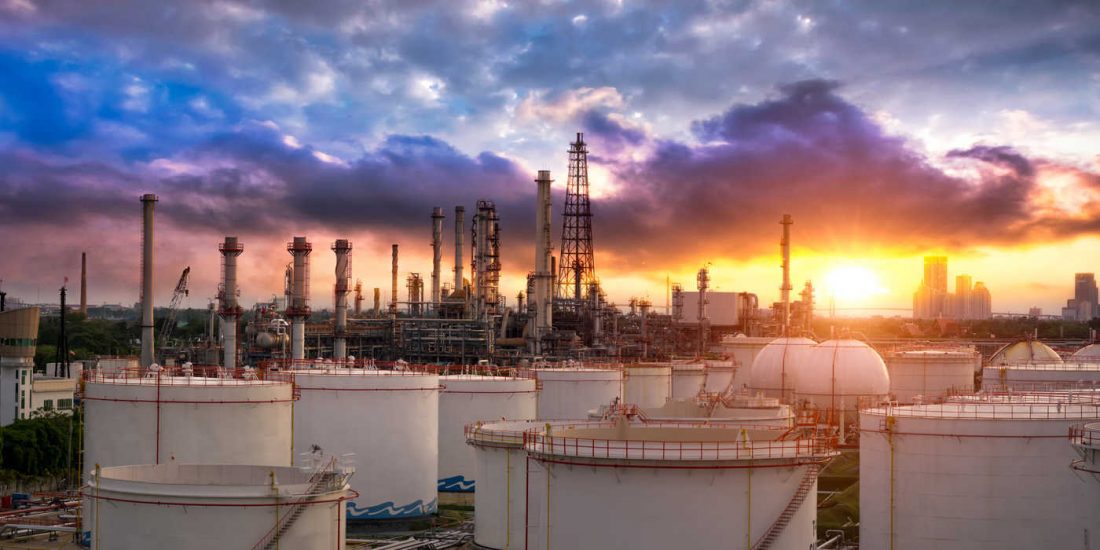
Some utility companies have been overlooking viable ways to generate more value from their gas and coal plants. How can they reduce costs and unplanned downtimes without increasing the risks?
Utilities are facing the difficult task of reducing operational and maintenance tasks without risking a loss in energy production. Achieving an equilibrium of asset maintenance, that is to say, without spending more and not interrupting production, is not only a constant challenge, but also a tricky balancing act.
Why is this a problem in gas and coal plants?
Change is a constant in the utilities sector. It is being led by some key factors:
- Coal plants are being shut down: Gas and coal assets are being replaced by renewable energies
- Decentralization: As coal and gas plants are being shut down, their replacements are not as large. Power generation is more evenly distributed.
- Digitalization: More computers and machinery is being interconnected, the sector is increasingly connected and consumers have more control than ever.
The above factors are intensifying the challenges the industry is facing, but there are also others: Smaller profit margins, increase in power generation flexibility, extended downtime costs and an increasingly older workforce.
The scenario is clear and as follows; as operating costs increase and profit margins decrease, how can utilities maximize their resources to obtain the highest possible value?
There are three main ways that artificial intelligence can help gas and coal plants:
Use AI to clear transaction data
Data in coal and gas plants is somewhat confusing, inconsistent and at times erroneous. Artificial intelligence solves the problem through correction automation, standardizing the precise nature of its data; the idea is that it can later be transformed in procesable information that translates into economic results.
An example of this would be the data in work orders that are manually registered by operators and are of irregular quality. To obtain information on this data, artificial intelligence processes the data in a natural language and uses other techniques to identify errors. Then it automatically suggests corrected amendments to better the precision and quality of that information.
AI understands the manufacturer and the model of the machine, what type of assets are involved, what the specifics are in the work done and written descriptions and commentaries of the operators. Having taken all these factors into account, AI determines what fields have to be corrected.
Working with corrected data, AI can go beyond errors and faulty work orders to reveal what resources are contributing to higher maintenance costs.
Optimizing maintenance strategies
With a detailed view of the data from work orders, it can now answer questions like: “Are my maintenance strategies as effective as I had hoped?” and “Is there a way I can reduce maintenance costs without incurring additional risks?”
Artificial Intelligence understands what is happening with your resources, it can precisely measure the effectiveness of the maintenance work that is being carried out, which helps in answering these key questions:
- Measure availability: “What is causing downtime in my resources?”
- Measure financial impact: “Which of my assets has the highest maintenance costs?”
- Based on real conditions: “What can I learn from the current condition of my resources?”
- Learn and continuously implement: “How can I measure the impact of the changes in my maintenance strategy?”
Once one realizes that resources can be problematic; optimization software can create and apply more financially responsible strategies, personalized for a company’s commercial interests.
Harness unexploited energy potential
AI helps recover energy sources that were in “the shade”, that is to say, the unexploited energy that a plant has: The idea is that by detecting strange and erratic behaviour in a plants most critical resources, and by predicting and preventing machine errors before they happen, a great deal of time and money will be saved.
Firstly, anomaly detection uses a model based on similarity, recognizes patterns, and notifies you when plant resources are not working as was hoped. It uses data sensors and environmental variables like temperature, vibrations, flows and other factors to create a multidimensional pattern from which it can detect variations. Once the operating conditions and circumstances are established, the motor knows what to do, if it has to send an alert signal or not.
Secondly, fault prediction engines can give a prognosys of the probability of future mishaps. Therefore, work stoppages and malfunctions can be avoided. Once it has established the frequency of a small malfunction, it can fix itself and therefore, avoid an unplanned and costly shutdown in the future.
Artificial Intelligence can inform you when immediate action is required. Combine this to optimized maintenance strategies based on work order data, the value for coal and gas plants is invaluable.